Tilt-Up & Precast Painting and Surface Preparation.
Concrete tilt-up walls demand a nuanced approach to painting, recognizing the unique challenges and product requirements these surfaces entail. Our expertise in selecting and applying the appropriate coatings ensures not only an aesthetically pleasing building but also one that stands up to the rigors of time and use, preventing common issues like peeling or blistering.
Concrete tilt-up walls demand a nuanced approach to painting, recognizing the unique challenges and product requirements these surfaces entail. Our expertise in selecting and applying the appropriate coatings ensures not only an aesthetically pleasing building but also one that stands up to the rigors of time and use, preventing common issues like peeling or blistering.


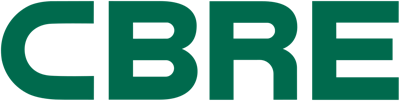
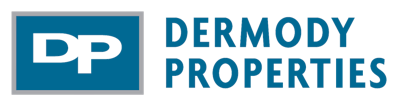

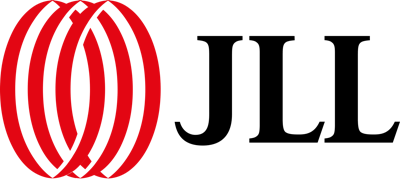

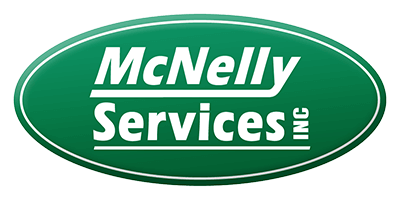



Tilt-up construction, a preferred method for erecting warehouses, distribution centers, and big-box retail stores, offers the significant advantages of time and cost savings. However, maintaining the structural and aesthetic integrity of these facilities is crucial to protect your investment against the natural wear and environmental challenges they face. Our specialized service is meticulously designed to address the unique requirements of tilt-up construction, ensuring not only an enhanced visual appeal but also robust protection against the elements.
At Painters USA, we pride ourselves on our meticulous attention to detail, from the initial assessment and surface preparation to the final application of coatings. Our team of expertly trained and certified professionals is adept in all facets of industrial cleaning, surface preparation, and painting techniques, ensuring that your tilt-up buildings are not only visually appealing but also protected against environmental and structural challenges. With our unmatched safety credentials and commitment to quality, partnering with us means entrusting your tilt-up construction to the best in the field.
Problems You Have That We Can Solve
Over time, tilt-up concrete surfaces may show signs of paint degradation, including peeling, blistering, or fading. This not only affects the building’s aesthetics but can also expose the structure to elements, leading to more serious damage.
The corrosion of embedded metals such as reinforcing steel is a common problem in concrete structures. Rust stains not only mar the appearance but can also compromise the structural integrity of your tilt-up buildings.
This white, powdery residue of salts can form on concrete surfaces that are not well-protected, causing aesthetic and structural issues over time. Effective cleaning and protective coatings are essential for preventing future efflorescence.
Cracks in tilt-up walls can be due to construction errors, shrinkage, or environmental factors. Addressing these cracks promptly can prevent further damage and maintain the structural integrity of the building.
Tilt-up concrete requires specific treatments to prevent water penetration, which can cause damage to the building’s interior and exterior over time.
Continuous exposure to UV radiation can cause the paint on tilt-up buildings to fade and deteriorate, affecting the building’s aesthetic appeal and surface protection.
Tune-up Your Tilt-Up Construction
Elevate the durability and aesthetic appeal of your tilt-up buildings with our specialized painting services. Our expertise in selecting the right coatings and techniques ensures your project withstands the test of time and elements. Ready for a transformation? Our team is here to guide you every step of the way.
Prepping, Priming and Painting
Every commercial or industrial painting project involves the “3 P’s” of prepping, priming, and painting. Neglecting any one of them creates a weak link that can show up and cause issues very quickly.
Prepping
Having worked on numerous tilt-up buildings in many different environments across the country, Painters USA will determine the best cleaning methods and repairs with the right high-strength mortars and non-shrink grouts. Commercial painting project that skip or shortcut this step are bound to fail, costing more time and money to fix or redo.

Priming
Painters USA uses quality, acrylic-based masonry sealers and primers on all exterior concrete tit-up walls for moisture protection. Water penetration contributes to rusting of embedded metal, efflorescence, and other issues. Acrylic masonry primers and sealers are designed for the alkalinity of fresh concrete, and they are water and stain repellent for long term protection from the elements.
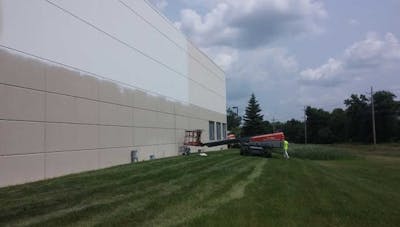
Painting
Poor surface preparation and the wrong paint for exterior masonry surfaces are the likely culprits of paint blistering, peeling, and other types of degradation. It’s important to balance cost and performance and use only quality, acrylic-based paints, which offer the necessary water resistance. Alternative paints may have compounds that decompose in reaction to moisture. Painters USA will always recommend the best products to help you reach the right balance.
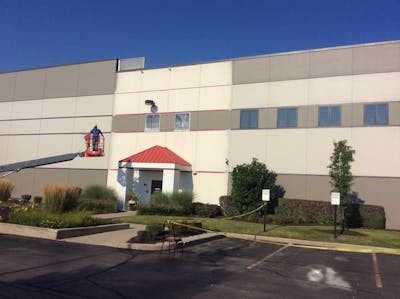
Protect Your Investment
Don’t let environmental stressors compromise your tilt-up construction. Our comprehensive painting solutions offer the protection your building needs against weathering, efflorescence, and corrosion. Safeguard your asset with high-quality coatings designed for resilience and longevity. Concerned about your building’s protection? Let’s address it together.
Why choose Painters USA?
Maintenance is disruptive. You need a team that gets in and out ASAP. That’s why we pride ourselves with our large, well-trained crews that meet your deadlines and minimize downtime – our speciality!
Being on-budget is as important as being on-time, so we prepare accurate estimates and bids for no unwanted surprises.
We aim to meet or exceed quality expectations, backed by warranties and recommending the best materials to balance performance and costs.
For convenience and single-point-accountability, we have the resources and capacity to work across multiple sites in the US, including remote / rural locations.
Our commitment to safety—backed by ISN RAVS Plus® status and an exemplary TRIR rating—reduces workplace hazards and legal / financial risks in your facilities.
Painters USA is fully licensed and insured, and our crews are full-time employees who have undergone thorough background checks.
We are happy to share client references based on your industry or facility challenges and goals for the greatest relevance to your situation.
As a woman-owned business, we can help you diversify and expand your supplier network.
Our happy clients. Both big and small
Enhance Operational Morale.
A properly-maintained facility reflects well on your business and boosts employee morale. Our tilt-up painting services not only improve the appearance of your building but also contribute to a positive work environment. Want to make a lasting impression on both your staff and clients? We’re ready to help you make that impact.
A properly-maintained facility reflects well on your business and boosts employee morale. Our tilt-up painting services not only improve the appearance of your building but also contribute to a positive work environment. Want to make a lasting impression on both your staff and clients? We’re ready to help you make that impact.
