Industrial and Commercial-Grade Epoxy Flooring Solutions.
Protect concrete floors with the right coating technologies for withstanding forklift traffic, chemical spills, and other destructive forces. Our flooring experts are committed to delivering customized solutions that meet your operational needs and compliance standards. Discover how our expertise can transform your environment.
Protect concrete floors with the right coating technologies for withstanding forklift traffic, chemical spills, and other destructive forces. Our flooring experts are committed to delivering customized solutions that meet your operational needs and compliance standards. Discover how our expertise can transform your environment.
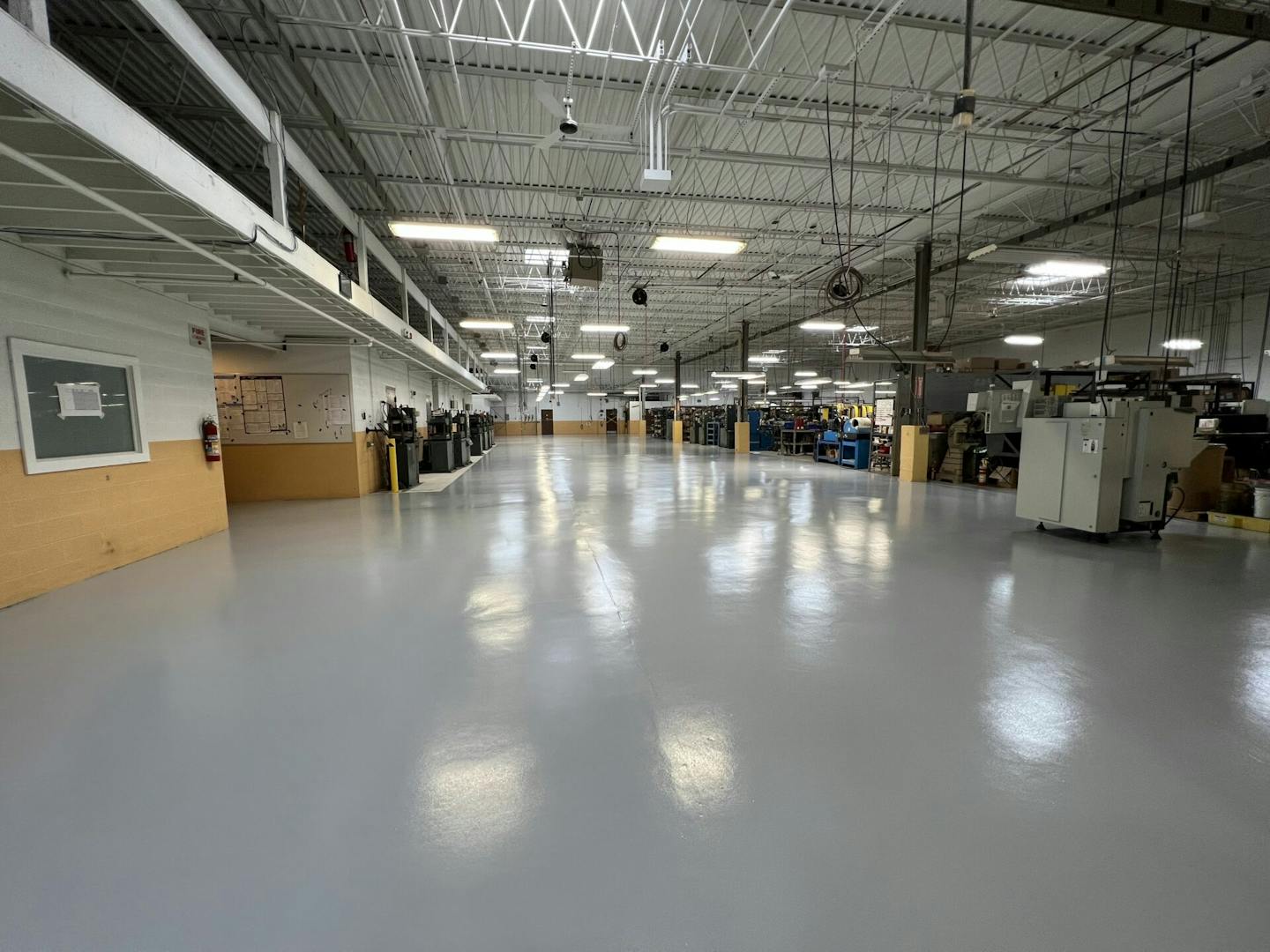
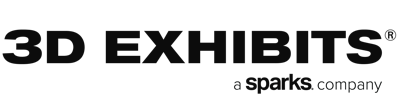

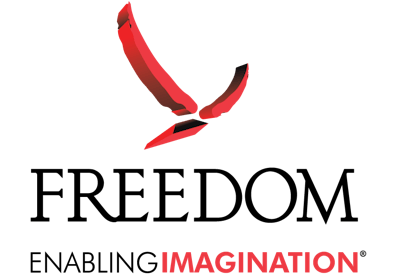

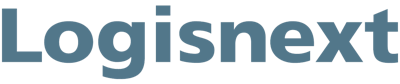
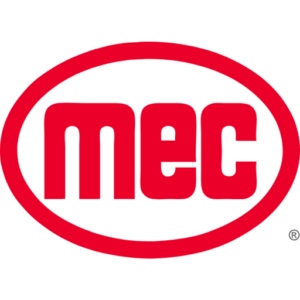
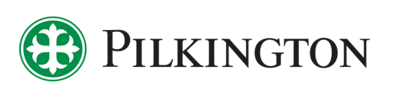
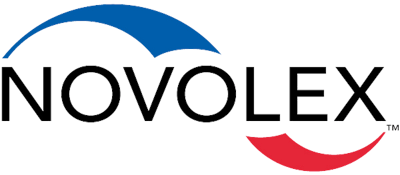
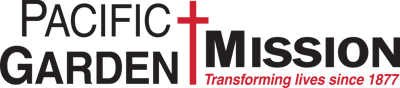
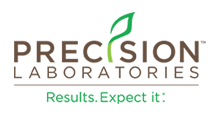
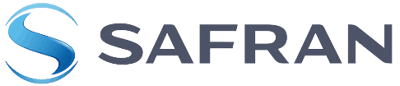
Epoxy flooring stands as a cornerstone for industries demanding not only a robust defense against the daily wear of heavy machinery and chemical spills but also a commitment to aesthetics and cleanliness. With a proven track record in enhancing operational efficiency, safety, and compliance across a multitude of settings, our epoxy flooring solutions are tailored to meet the rigorous standards of manufacturing, warehousing, and commercial environments.
At the heart of our service lies a dedication to providing a seamless, durable, and visually appealing floor that withstands the test of time and operation, ensuring your facility operates smoothly and safely. Let us equip your space with a flooring solution that reflects your commitment to quality and efficiency.
See Epoxy Flooring Projects We’ve Done
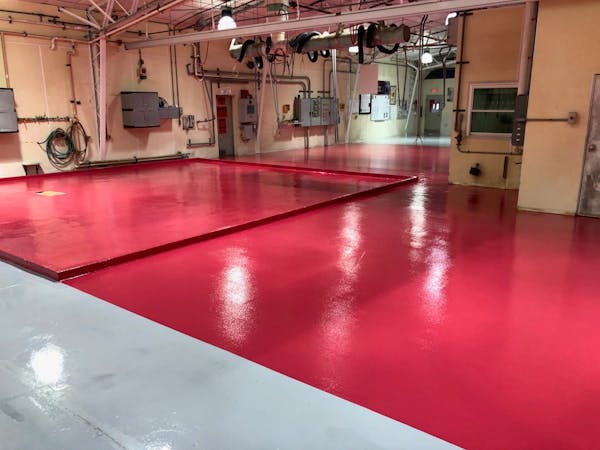
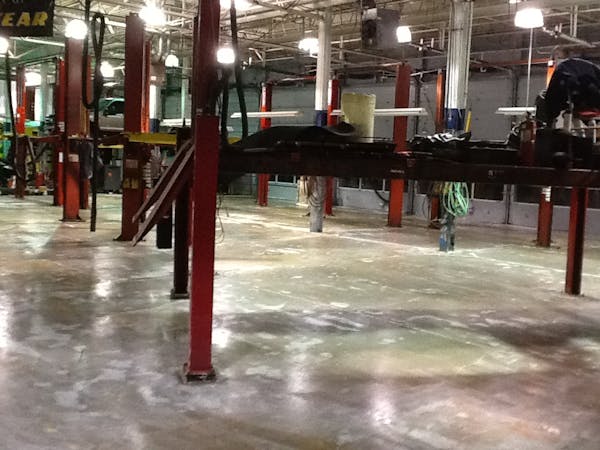
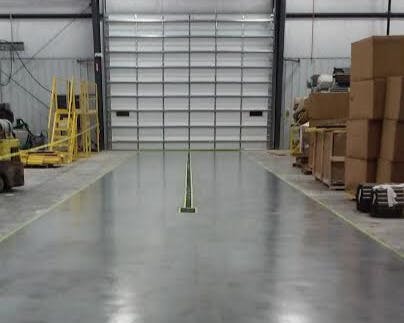
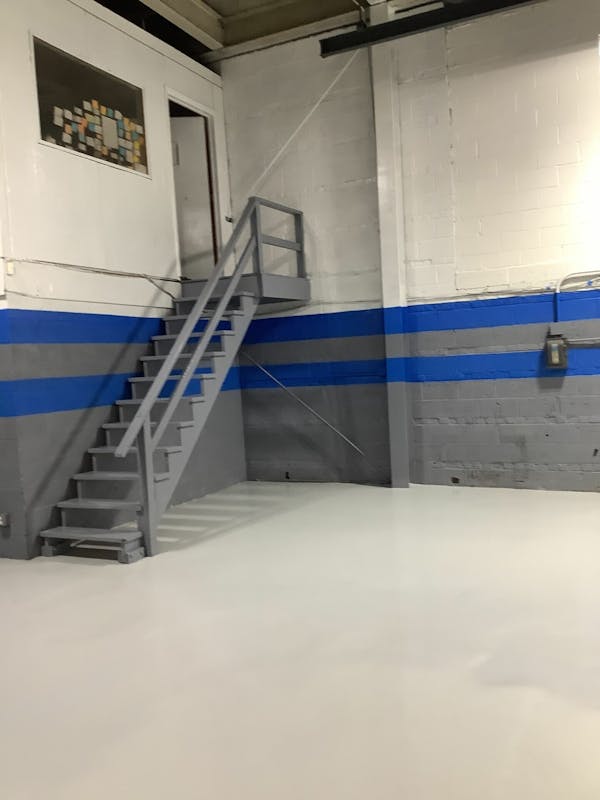

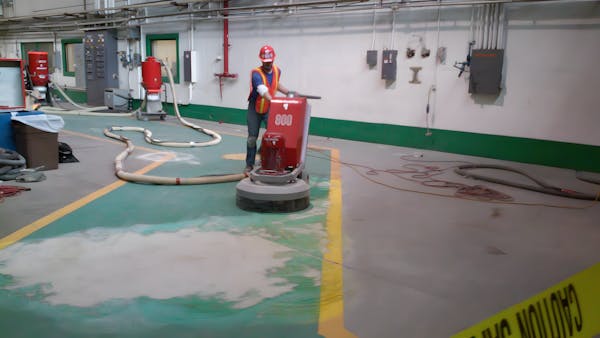

Get Your Project Done With Minimal Downtime
We work around the clock to ensure your business continues uninterrupted. From evenings to holidays, we can work around your planned downtime. When it comes to shutdown work, we’re pros.
Problems You Have That We Can Solve
With regular audits and inspections, no food company can afford to be non-compliant with SQF and other regulations. Professional epoxy flooring delivers superior food grade protection from biological, chemical, and physical hazards.
If your production processes involve regular use of solvents, acids, and other chemicals, you understand the corrosive force these materials have on concrete surfaces. Specialized epoxy coating systems offer excellent protection for preserving structural integrity.
Forklifts wreak havoc on concrete flooring in warehouses, distribution centers, and manufacturing facilities. On the flip side, control joints and other seams can cause major damage to forklifts! Reduce and prevent these physical hazards with seamless epoxy flooring systems.
If slips and falls are a concern, different textures and anti-slip additives can be incorporated into the epoxy floor system, plus epoxy is a durable option for floor striping and markings to safely guide traffic and workflow.
Flooring maintenance is a disruptive process, best contained with fast return to service and solutions that are long-lasting. Painters USA delivers both with our epoxy floor system expertise and many years of projects delivered on-time.
Aesthetics have become very important in modern industrial facilities, especially in large corporations with internal standards for all their locations. Painters USA’s epoxy flooring services will deliver a bright, pleasant look to your facility!
Why choose Painters USA?
Maintenance is disruptive. You need a team that gets in and out ASAP. That’s why we pride ourselves with our large, well-trained crews that meet your deadlines and minimize downtime – our speciality!
Being on-budget is as important as being on-time, so we prepare accurate estimates and bids for no unwanted surprises.
We aim to meet or exceed quality expectations, backed by warranties and recommending the best materials to balance performance and costs.
For convenience and single-point-accountability, we have the resources and capacity to work across multiple sites in the US, including remote / rural locations.
Our commitment to safety—backed by ISN RAVS Plus® status and an exemplary TRIR rating—reduces workplace hazards and legal / financial risks in your facilities.
Painters USA is fully licensed and insured, and our crews are full-time employees who have undergone thorough background checks.
We are happy to share client references based on your industry or facility challenges and goals for the greatest relevance to your situation.
As a woman-owned business, we can help you diversify and expand your supplier network.
Our happy clients. Both big and small
Our happy clients. Both big and small
Our happy clients. Both big and small
Our happy clients. Both big and small
Our happy clients. Both big and small
Improvements for Every Aspect
Improve the safety, functionality, and aesthetic appeal of your workspace with our custom epoxy flooring solutions. Whether you’re aiming to meet stringent compliance standards or simply revitalize your facility’s look, our expert team is here to guide you through every step. Don’t settle for less–unlock the full potential of your space today.
Questions you should be asking
A number of different factors should be assessed, plus unique traits that apply to your business or facility:
- Traffic patterns and volume
- Condition of concrete substrate
- Environmental factors like thermal shock and chemical exposure
- Compliance with various regulations and standards
- Typical operational schedules
Epoxies and polyurethanes are both thermosetting polymers, made by irreversibly hardening a soft solid or viscous liquid by heat or mixing with a catalyst. They work well together, and the most durable coating systems usually consist of an epoxy primer, an epoxy build-coat, and a polyurethane topcoat. Epoxy is preferred for priming concrete substrates and providing build or thickness to correct for minor imperfections or uneven floors. Polyurethanes enhance performance and aesthetics, protect from yellowing, improve chemical and abrasion resistance, and offer more finishing options.
Curing and setting times vary. While most experts agree that epoxy is safe to walk on after about 25 hours, epoxy cure times can range from 12-18 hours to 36-72 hours for a return to normal operational traffic. It takes about a week for most epoxies to reach full chemical cure. For results that are long-lasting and most durable, it’s important to discuss your return to service needs, as rushing the curing process can lead to long-term performance issues.
When discussing painting and coating in the US, a mil is not a millimeter (mm) but 1/1000th of an inch, based on the English or Imperial System used in the United States. A thickness of 20 mils means the coating is 20/1000 inches thick.
As for how many mils are needed for epoxy floor coatings, it could range from a few mils to as thick as 40-50 mils. The variables used to assess mil thickness include condition of the concrete substrate, performance demands, the operational environment, manufacturer recommendations for the specific coating product, and time and budget constraints.
When the right coatings are specified and all steps of the installation process—substrate repairs and surface prep, coating application, cure time—are done correctly by experienced industrial floor coating professionals, epoxy floor coatings can last well over ten years of normal operations, with proper cleaning and maintenance.
Minimize Downtime, Maximize Efficiency.
Understandably, time is of the essence in your operations. Our efficient and effective flooring services are geared towards minimizing downtime and getting your facility back to full capacity swiftly, without compromising on quality or safety. Ready to enhance your operational efficiency with minimal interruption? Connect with us today.
Understandably, time is of the essence in your operations. Our efficient and effective flooring services are geared towards minimizing downtime and getting your facility back to full capacity swiftly, without compromising on quality or safety. Ready to enhance your operational efficiency with minimal interruption? Connect with us today.
