Corrosion Control and Rust Removal for Your Industrial Equipment.
We provide specialized services aimed at prolonging the life of your assets, lowering maintenance costs, and bolstering safety. Our NACE-certified professionals possess unrivaled expertise in rust and corrosion control, guaranteeing that your equipment and infrastructure are kept in optimal condition, shielding them from the forces of the environment.
We provide specialized services aimed at prolonging the life of your assets, lowering maintenance costs, and bolstering safety. Our NACE-certified professionals possess unrivaled expertise in rust and corrosion control, guaranteeing that your equipment and infrastructure are kept in optimal condition, shielding them from the forces of the environment.

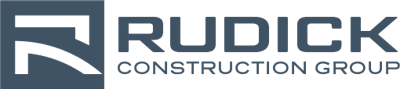
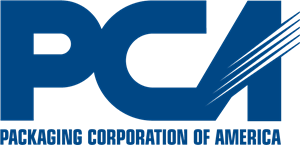

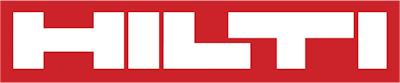
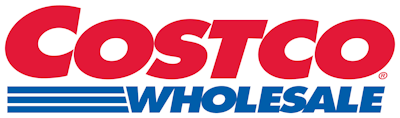
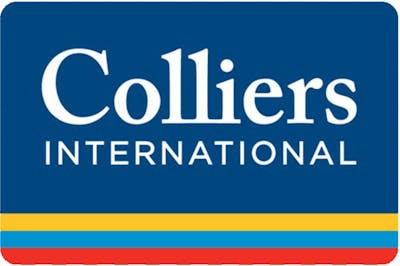
Our specialized services stand as your first line of defense in combating the relentless force of corrosion and rust in your industrial environments. Corrosion not only threatens the structural integrity of steel and other equipment, but also poses significant risks to operational efficiency and safety.
Painters USA offers a comprehensive three-step approach to corrosion and rust control, to ensure your equipment and structures are not just protected, but also primed for long-term resilience and reliability.
- Identify early issues and vulnerabilities to nip them in the bud.
- Properly clean and prepare metal surfaces and adjacent areas.
- Properly apply the best coating technology for your unique requirements
If rust and other forms of corrosion are an ongoing issue in your facility, working with a commercial / industrial contractor like Painters USA is important. We have both decades of experience and expertise validated by coating industry certifications from NACE and SPCC, now together as the Association for Materials Protection and Performance or AMPP.
See Corrosion Control Projects We’ve Done
Ensure Safety and Compliance
Corrosion can pose significant safety risks and compliance challenges. Let us help you create a safer working environment and stay ahead of regulatory demands with our advanced corrosion prevention services. Take the proactive step towards protecting your employees and meeting industry standards today.
Problems You Have That We Can Solve
Corrosion doesn’t just attack the surface; it seeps deep, dramatically slashing the operational lifespan of your vital machinery. With a combination of our blasting techniques and available coatings we increase your equipments lifespan.
When rust takes hold, it weakens structures, turning them into possible hazards and safety risks. Our services and coatings help keep rust and corrosion at bay, safeguarding against potential accidents.
Corrosion diminishes the professional look of your facilities. Our corrosion control services do double duty: stopping rust in its tracks, and revitalizing the aesthetic appeal of your facilities, ensuring they stand out for the right reasons.
Corroded surfaces are harder to clean and maintain. Our protective solutions streamline these tasks. By applying a fresh, protective coat after rigorous blasting, we transform surfaces into ones that are easy to keep clean and maintain.
Before and Afters of Our Work
Why choose Painters USA?
Maintenance is disruptive. You need a team that gets in and out ASAP. That’s why we pride ourselves with our large, well-trained crews that meet your deadlines and minimize downtime – our speciality!
Being on-budget is as important as being on-time, so we prepare accurate estimates and bids for no unwanted surprises.
We aim to meet or exceed quality expectations, backed by warranties and recommending the best materials to balance performance and costs.
For convenience and single-point-accountability, we have the resources and capacity to work across multiple sites in the US, including remote / rural locations.
Our commitment to safety—backed by ISN RAVS Plus® status and an exemplary TRIR rating—reduces workplace hazards and legal / financial risks in your facilities.
Painters USA is fully licensed and insured, and our crews are full-time employees who have undergone thorough background checks.
We are happy to share client references based on your industry or facility challenges and goals for the greatest relevance to your situation.
As a woman-owned business, we can help you diversify and expand your supplier network.
Protect Your Investment Today
Don’t let corrosion compromise the lifespan and efficiency of your equipment. Our experts in corrosion and rust control are here to provide solutions tailored to your needs. Ready to enhance the durability of your facilities? We’re here to guide you every step of the way.
Our happy clients. Both big and small
Get Your Project Done With Minimal Downtime.
We work around the clock to ensure your business continues uninterrupted. From evenings to holidays, we can work around your planned downtime. When it comes to shutdown work, we’re pros.
We work around the clock to ensure your business continues uninterrupted. From evenings to holidays, we can work around your planned downtime. When it comes to shutdown work, we’re pros.
